Window Replacement is one of the best ways to improve your home’s energy efficiency and protect it from moisture, pests and weather damage. But how do you know when it’s time?
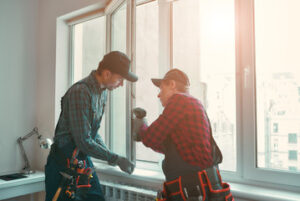
The answer depends on whether your windows are functioning properly. If they aren’t, you should consider whole-window replacement. Contact Window Replacement Austin for professional help.
The frame is the structural component of a window, connecting the glass panes and protecting them from outside elements. It can also enhance the appearance of your home, adding visual appeal and creating a sense of style. Window frames are available in a variety of materials, each with unique advantages and benefits. Durability, maintenance requirements and energy efficiency are important factors when deciding on the best frame for your home.
There are several different types of frame materials to choose from, including wood, fiberglass and aluminum. Each offers a unique aesthetic and can complement your home’s design. Fiberglass and aluminum frames are highly durable and energy efficient. These frames are also resistant to moisture and rot and can withstand harsh weather conditions. They are lightweight, and can be painted to match your home’s décor.
Wood frames are a popular choice because of their natural appearance and classic beauty. They are also highly insulating and can be refreshed with a fresh coat of paint or stain. However, wood is vulnerable to moisture and insect damage, and requires regular upkeep.
Aluminum frames are strong and lightweight, making them a good option for larger windows. However, they are not as energy-efficient as other materials and can conduct heat. To improve their insulating capabilities, you can add thermal breaks to aluminum frames. These are resins and insulators that are inserted in the hollow parts of the frame where heat usually travels.
Composite frames are a combination of wood and either fiberglass or aluminum, and offer the best of both worlds. They are highly insulating, resist warping and rotting, and can be painted to match your home’s color scheme. They are also more resistant to humidity and condensation than wood, but can still deteriorate if exposed to prolonged direct sunlight.
It is important to remember that a quality window frame is an investment, and should be treated as such. A well-made frame will last for years and can increase the value of your home. It should also be easy to maintain and durable enough to withstand various weather conditions.
Glass
The glass is one of the most important aspects of a window or door. It allows natural light to enter a home or office, while offering privacy and security. It can also contribute to energy efficiency and overall performance. Professionally installed glass can reduce utility bills and add a boost to your property’s value.
Aesthetics: Cracked and outdated windows are unattractive, and can diminish the curb appeal of a building or residence. Replacing broken glass can give a fresh new look, improving aesthetics and adding value.
Safety: During a break, tempered glass shatters into blunt pieces rather than sharp shards, making it safer for you and your family. It’s also a better option for high-traffic areas like sliding doors or windows located near the ground. Laminated glass consists of two layers of glass with a layer of plastic in between, providing an extra level of protection against break-ins and other damage.
Efficiency: Poorly maintained and damaged window glass can contribute to energy loss, resulting in higher utility bills. Replacing glass with higher-performing options can improve insulation, reducing energy costs and lowering your environmental footprint.
A good way to measure glass quality is by its U-Factor, which measures how well the window keeps heat inside in winter and out in summer. The lower the number, the more efficient the window is. Other factors to consider are visible light transmission, UV transmittance, and thermal conductivity. Experts can guide you in selecting a type of glass that suits your specific needs and design preferences. They can even help you choose frosted or decorative glass to complement your style. They can also ensure that the replacement glass is properly fitted and sealed, minimizing downtime and preventing leaks and other issues. They’re also well-versed in local regulations, ensuring that your window meets all requirements. A well-maintained window can increase your property’s value and enhance your comfort. A faulty window or door can cause damage and lead to costly repairs. Window replacement is the best option to prevent these problems and ensure that your property’s windows and doors are functioning at their best.
Design
A well-designed window is a harmonious blend of form and function. Aside from adding style and enhancing your living space’s interior aesthetic, windows play a pivotal role in shaping your home’s energy efficiency and indoor comfort. As a homeowner, you have several options when it comes to window design, from frame materials and glazing to the size of the panes. With these factors in mind, you can make the right decision for your home’s specific needs.
The window frame material and color have a major impact on the overall appearance of your house. Wood, vinyl, and fiberglass are the most popular frame materials. Traditional wood frames offer timeless beauty and superior insulating qualities. However, they require regular maintenance to keep them in good condition. Vinyl and fiberglass frames are low-maintenance and are available in various colors to match your home’s exterior.
You can also choose between symmetrical and radial designs. Symmetrical windows feature identical elements on both sides of a central line, while radial ones are arranged around a center point. If you choose a symmetrical window design, it is important to take accurate measurements and ensure that the windows are properly aligned. This will prevent any structural issues down the line and maintain a consistent aesthetic.
Your choice of glass also plays a significant role in the window’s visual appeal and functionality. Options like tinted, frosted, and low-E glass allow you to customize the window’s appearance while providing benefits such as privacy and energy efficiency. Additionally, you can select between double- and triple-pane windows. Double-pane windows offer increased insulating properties while triple-pane windows offer even greater energy efficiency.
When choosing a window, it is important to consider your home’s orientation and lighting conditions. For example, south-facing windows can maximize sunlight while north-facing windows provide a more diffused light that can be beneficial for spaces that need less direct sunlight. Additionally, you should consider the type of ventilation your home requires. If your home is located in a humid climate, you may want to opt for air-tight windows with built-in storm doors.
Installation
When a window is damaged beyond repair, it may require replacement to restore its function and enhance your home’s appearance. In addition, modern double- or triple-pane windows with low-E coatings and insulated frames are often more energy efficient than older single-pane ones. These features can reduce your energy costs and enhance comfort without compromising the integrity of your historic home’s architectural style.
Whole-window replacement is also often necessary to address issues that are not repairable, such as poor ventilation, water leakage, rotting wood or a broken sash or frame. Older homes in particular may contain lead paint that poses health risks if disturbed during a window replacement project. Choosing a certified contractor who follows best practices for working with lead-based paints is essential to ensure your family’s safety.
Prior to the installation date, prepare by moving any furniture or decorations away from your windows. This includes curtains, blinds, plants and anything hanging on or in front of the windows. If there is a window near the front door, clear a pathway to it and move any items that might get in the way of accessing the doors.
It is also important to find out if the installer requires a permit and what their policies are about working in inclement weather. If they are not able to work in rain or snow, this can cause delays and possibly force them to come back at a later time.
Once the old window is removed, the contractors will make sure the new one fits properly by adjusting its position in the frame with shims. They may even use a level to check the corners of the window are square and plumb. If they find any areas that are not properly sealed, they can apply caulk or other caulking to help prevent air leaks and water damage.
After all the caulking and sanding is done, the trim can be applied and painted to complete the installation. Be sure to ask your contractor if this is included in the quote. If not, it is an additional cost. It is also a good idea to have your windows inspected after installation for quality assurance.